The Impact of AI and IoT on the Future of Smart Manufacturing: A Deep Dive
Not long ago, factories ran on manual labor and mechanical systems that required constant human intervention. But today? The power of AI and IoT has transformed Smart Manufacturing, enabling machines to foresee failures before they occur, alter production lines in real-time, and operate supply chains with near-zero waste. And the numbers prove it.
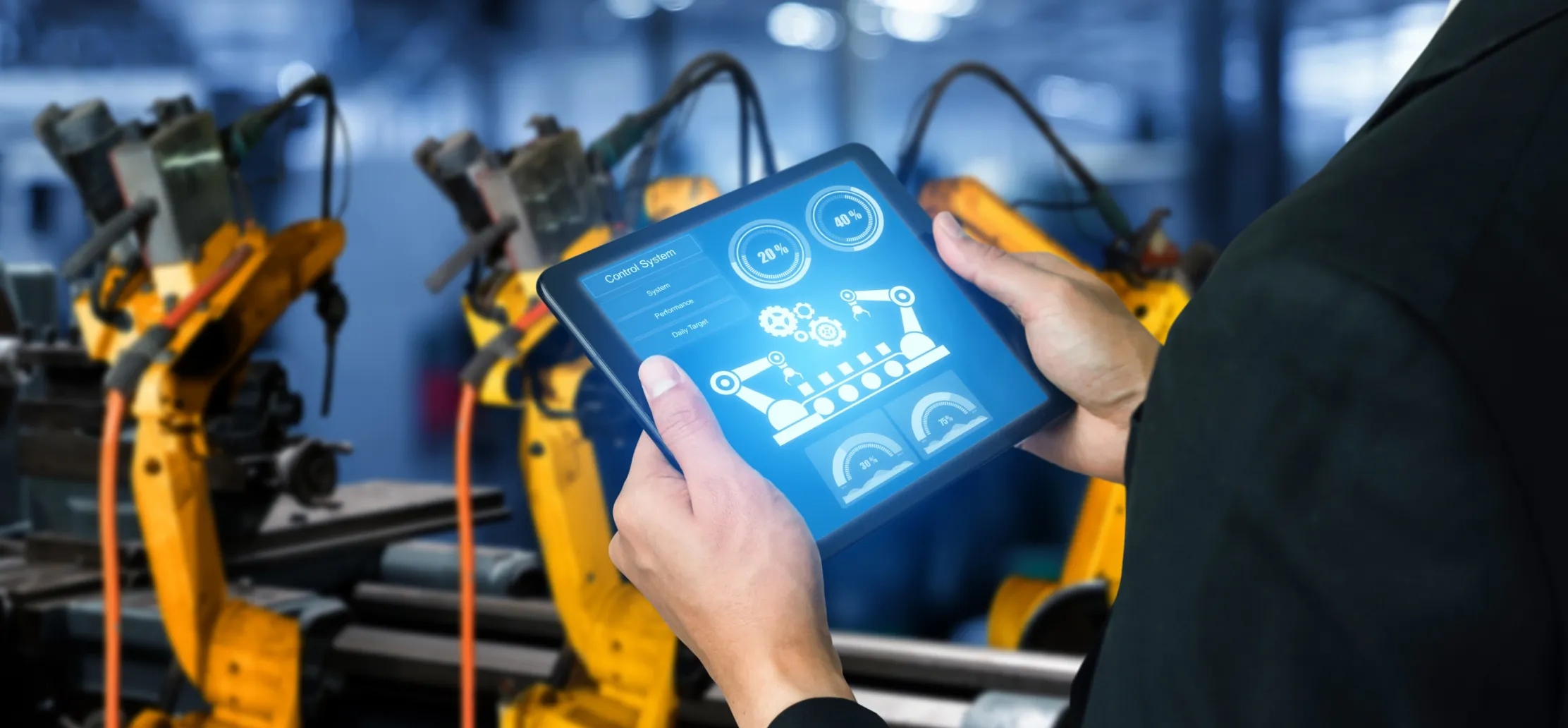
The global IoT in manufacturing market was worth $27.8 billion in 2018, and it’s on track to hit a staggering $452.27 billion by 2032. With a 22.1% CAGR, the shift toward Smart Manufacturing isn’t just happening—it’s accelerating at an unprecedented pace.
A fusion of AI, IoT, and real-time data sharing that’s turning traditional factories into intelligent, self-optimizing ecosystems. From predictive maintenance that cuts downtime in half to IoT-driven automation that enhances efficiency, manufacturers are seizing new opportunities for growth and innovation. Even small and medium enterprises (SMEs) are jumping on board, leveraging these technologies to cut costs, boost productivity, and streamline operations.
Let’s explore how AI and IoT are revolutionizing Smart Manufacturing and what it means for the future of the industry.
The Impact of AI and IoT on Manufacturing:
To understand why AI and IoT are revolutionizing Smart Manufacturing, let’s break down what these technologies do.
Artificial Intelligence (AI) is all about enabling machines to learn, adapt, and make decisions. AI in Manufacturing is used for predictive maintenance, quality control, and process optimization, helping factories run more efficiently with fewer disruptions.
On the other hand, the Internet of Things (IoT) connects physical devices—like machines, sensors, and production systems—to the Internet, allowing them to collect, analyze, and share data in real-time. This means manufacturers can track operations, monitor machine health, and gain insights that were once impossible to capture.
When AI and IoT work together, they create intelligent, self-optimizing ecosystems within factories. IoT devices gather vast amounts of data from machines, and AI analyses that data to predict failures, optimize workflows, and automate decision-making. This fusion of AI and IoT isn’t just about improving processes—It’s about transforming the manufacturing industry into a smarter, more agile one
Revolutionize Manufacturing With AI and IoT to Enhance Efficiency and Quality
Discover how smart technologies are transforming manufacturing
Success Stories: How AI and IoT Are Revolutionizing Manufacturing
Let’s dive into some of the best examples of AI and IoT revolutionizing the manufacturing industry.
Case Study 01: Siemens’ Predictive Maintenance with AI and IoT
Industry: Manufacturing Automation & Digitalization
Challenge: Siemens needed to optimize manufacturing operations, minimize unplanned downtime, and improve equipment reliability across its global facilities.
Solution: Siemens implemented an AI-driven predictive maintenance system powered by IoT and Big Data:
- IoT Sensors: Monitored real-time data (temperature, pressure, vibration).
- MindSphere Platform: Processed and analysed data using machine learning for anomaly detection.
- Predictive Maintenance Models: Forecasted potential failures, allowing proactive repairs.
- Visualization Dashboards: Provided real-time insights for data-driven decision-making.
Results:
- Reduced downtime with proactive maintenance
- Lower maintenance costs through optimized resource allocation
- Improved equipment reliability, boosting overall efficiency
Siemens effectively improved Smart Manufacturing operations by incorporating AI, demonstrating how Digital Transformation in Manufacturing can produce long-term efficiency and cost benefits. Read the full article here.
Case Study 02: ASUS AIoT – Revolutionizing Smart Manufacturing with AI
Industry: Smart Manufacturing & AI-driven Automation
Challenge: ASUS aimed to enhance manufacturing productivity by integrating AI and IoT for automated quality inspection and efficiency improvements.
Solution: ASUS introduced AISVision, an AI-powered computer vision system that streamlines Automated Optical Inspection (AOI):
- AI-Powered Computer Vision: Detects defects in real-time for precise quality control.
- Flexible AI Model Training: Enables manufacturers to train and deploy custom AI models within minutes.
- Reduced Workload: Cuts manual inspection efforts by 80%, improving speed and accuracy.
Results:
- Higher productivity with automated defect detection
- Significant cost savings by reducing manual inspection efforts
- Improved product quality with real-time AI-powered monitoring
ASUS is driving Smart Manufacturing forward by integrating AI in Manufacturing, enabling businesses to embrace Digital Transformation in Manufacturing for higher efficiency and accuracy. To read the case study in-depth, click here.
Case Study 03: GE is Transforming Manufacturing with Digital Twins
Challenge: GE wanted to improve efficiency, reduce downtime, and optimise production. The goal was to simulate real-world operations, predict potential issues, and fine-tune processes before they caused disruptions.
Solution: GE introduced Digital Twin Technology, creating AI-powered virtual models of their machines and processes. These digital replicas help monitor performance, detect inefficiencies, and refine operations.
Key applications include:
- AI-driven predictive analytics track over 7,000 critical assets, helping manufacturers prevent failures before they happen.
- Simulates the best production methods, cutting waste by up to 75% and improving throughput by 5-20%.
- Provides real-time visual data, enabling smarter decision-making in operations and maintenance.
Results:
- $1.6 billion saved by preventing equipment failures
- Faster and more efficient production with AI-driven process improvements
- Fewer defects and higher-quality output, enhancing customer satisfaction
3 Big Ways AI and IoT Are Changing Manufacturing for the Better
1. Enhanced Operational Efficiency:
Smart Manufacturing is transforming the industry by making factories more efficient and cost-effective. With AI in Manufacturing and IoT working together, manufacturers can now analyze data in real-time, predict issues before they happen, and automate key processes.
IoT-connected machines generate massive amounts of data, and AI turns that data into actionable insights—helping businesses reduce waste, speed up production, and cut costs. This means fewer delays, smarter workflows, and better product quality, all with minimal manual intervention.
2. Predictive Maintenance
Equipment failures can slow down production and drive up costs, but Digital Transformation in Manufacturing is changing the game. With predictive maintenance, businesses can spot issues before they turn into costly breakdowns.
IoT sensors constantly track machine performance, and AI analyses this data to detect early warning signs of failure. This proactive approach keeps operations running smoothly, extends equipment life, and improves workplace safety.
3. Quality Assurance
AI-powered Quality control is making vision systems faster and more reliable. These systems catch defects, ensuring only high-quality products make it to market.
In the past, inspections relied on human oversight, which often led to missed errors and inconsistencies. Now, AI-driven computer vision technology scans thousands of products per minute, detecting even the smallest flaws.
Integrate AI and IoT to Optimize Operations, Prevent Downtime, and Enhance Quality
Unlock the future of smart manufacturing with game-changing innovations
Challenges on the Path to Smart Manufacturing:
While Smart Manufacturing powered by AI in Manufacturing and IoT is transforming industries, it comes with its own set of challenges.
Data Security Concerns
With interconnected systems continuously exchanging data, cybersecurity becomes a top priority. Manufacturing facilities handle sensitive information, including production data, intellectual property, and operational insights.
Implementing robust cybersecurity protocols, encryption, and access control mechanisms is essential to safeguard critical data.
Integration Complexities
Many manufacturers still rely on legacy systems that were not built to support modern AI-driven and IoT-enabled solutions. Integrating new digital technologies with these older infrastructures can be challenging due to compatibility issues, high costs, and operational disruptions.
A strategic approach involving gradual upgrades, scalable architectures, and cloud-based solutions can help businesses transition smoothly into Smart Manufacturing without hampering existing operations.
Skill Gaps in the Workforce
The adoption of AI in Manufacturing and IoT demands a workforce skilled in data analytics, automation, and AI-driven decision-making. However, many employees lack the necessary expertise to operate and maintain these advanced systems.
To bridge this gap, companies must invest in upskilling programs, AI training workshops, and partnerships with tech institutions to equip their workforce with the skills needed for a digitally transformed manufacturing environment.
What’s Next? The Future of AI and IoT in Manufacturing
The future of AI in Manufacturing and IoT is shaping up to be faster, smarter, and more autonomous. As technology advances, manufacturers are moving toward real-time decision-making, ultra-fast connectivity, and self-optimizing production lines.
1. Edge Computing
Manufacturing generates enormous amounts of data, but sending it all to the cloud can cause delays. Edge computing solves this by processing data directly at the source—on the factory floor. This means real-time insights, quicker responses, and better efficiency.
2. 5G Connectivity
With 5G networks, manufacturers can connect machines, sensors, and AI systems with lightning-fast speed and minimal lag. This enables real-time monitoring, automated processes, and smarter decision-making.
3. Autonomous Production Lines
The power of AI-driven automation uses real-time data and predictive analytics, which helps the factories to self-correct, minimise waste, and maximise efficiency. This means fewer delays, lower costs, and higher-quality products.
Expert Insights: What Industry Leaders Are Saying
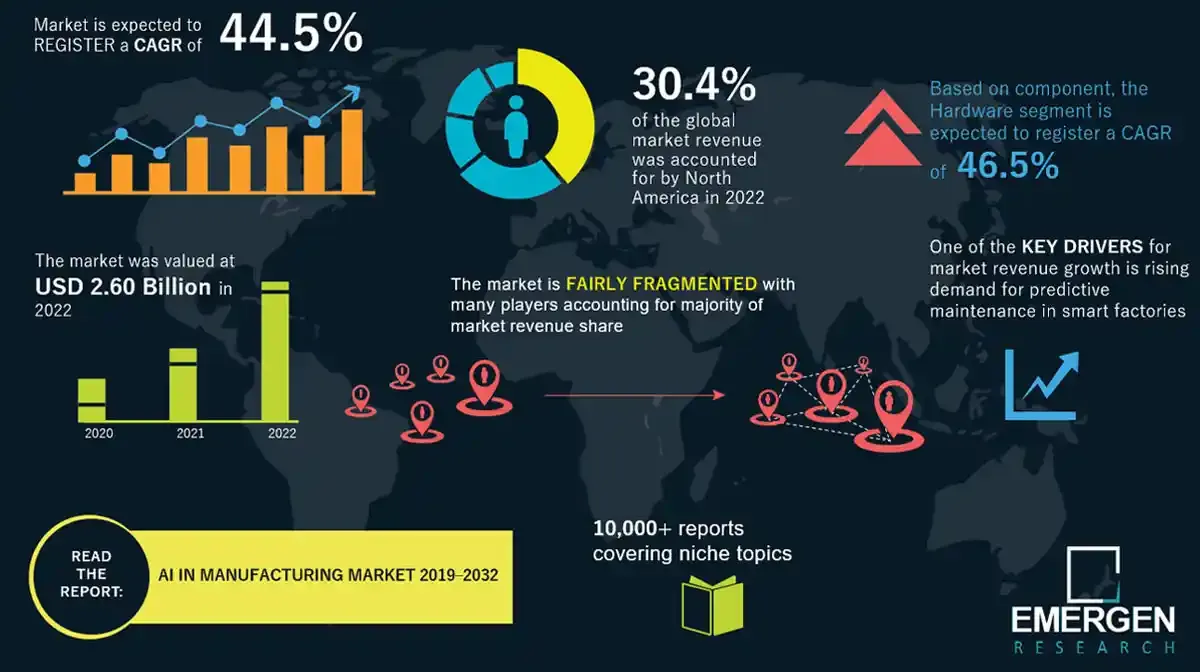
Manufacturing is evolving rapidly, and Generative AI is the latest technology, making a strong impact. While AI has already transformed industries like finance and healthcare, it is now gaining traction on the shop floors of manufacturing plants.
Many companies are experimenting with Generative AI, running pilot projects to see how it can improve operations. The potential is huge—AI is already enhancing design innovation, quality control, predictive maintenance, and production efficiency. As technology advances, these applications will become even more powerful.
Leading manufacturers like Eaton, Bosch, ABB, and Siemens have started integrating AI into their production systems to improve efficiency and reduce downtime. The push for digital transformation is fueling AI adoption, but challenges like skilled labor shortages and data security concerns still need to be addressed.
Top executives believe AI and IoT are making factories smarter, faster, and more efficient.
Experts say that AI in the manufacturing market is growing rapidly. In the coming years, 5G connectivity, Edge Computing, and self-learning production lines will become the norm. AI-powered quality control systems will also help detect defects with near-perfect accuracy, improving overall product standards.
The message is clear: Smart Manufacturing is the future. Companies that implement Digital Transformation in Manufacturing today will have a competitive advantage in the future.
Conclusion
Manufacturing is changing fast, and if you're not keeping up, you might find yourself falling behind. AI and IoT are already making a huge difference, helping businesses run smoother, cut costs, and make smarter decisions. Sure, it can be tricky to integrate these technologies, but the benefits—think higher efficiency and better decision-making—make it worth the effort.
In this blog, we've explored how AI and IoT are transforming manufacturing, with real-world success stories, challenges, and what’s coming next. The companies jumping on board with these technologies are seeing some seriously impressive results, from predictive maintenance to fully autonomous production lines.
The key takeaway?
To stay competitive, you need to adapt now, not later.
At TRooTech, we’re here to help you make that leap. With highly vetted developers, we help you to integrate AI and IoT into your processes or custom software solutions to improve your operations.
Get a custom quote from us today.
FAQs
Small and medium-sized manufacturers can start by focusing on specific use cases like predictive maintenance, inventory management, or quality control. Cloud-based AI solutions and cost-effective IoT devices eliminate the need for heavy infrastructure investments. Many AI/ML development services also offer scalable solutions, allowing businesses to integrate technology gradually based on their needs and budget.
The cost depends on factors like deployment scale, technology complexity, and current infrastructure. Large-scale automation projects can be expensive, but smaller manufacturers can start with cloud-based AI tools, smart sensors, and outsourced software development services to keep costs manageable. Over time, AI-driven efficiency improvements help reduce operational expenses and downtime, offering a strong return on investment.
Hiring a developer can be helpful, especially for custom AI and IoT solutions. However, businesses can also outsource software development or partner with AI/ML development service providers to implement scalable solutions without hiring a full-time team. Many cloud-based platforms now offer AI tools with minimal coding requirements, making implementation more accessible.
The main challenges include data security risks, high initial costs, system integration with existing infrastructure, and a lack of skilled workforce. AI and IoT require strong cybersecurity measures to protect sensitive manufacturing data. Additionally, companies must upskill employees or hire experts to manage and optimize these technologies effectively. Overcoming these hurdles requires a strategic approach and gradual adoption.